課題解決・導入事例
フィルター部品用小箱包装ライン
- 対象ワーク
- フィルター部品
- 対象ワークサイズ
- Φ60×H50~Φ75×H110
- 箱サイズ
- ①W75×L75×H94 ②W80×L80×H112 ③W67×L67×H85 ④W83×L83×H150 ⑤W79×L79×L90
- 箱種類
- 天側:3枚フラップ差し込み 地側:ワンタッチ
- 生産能力
- 常用15箱/分
- 納入業界
- 工業
全体ライン工程
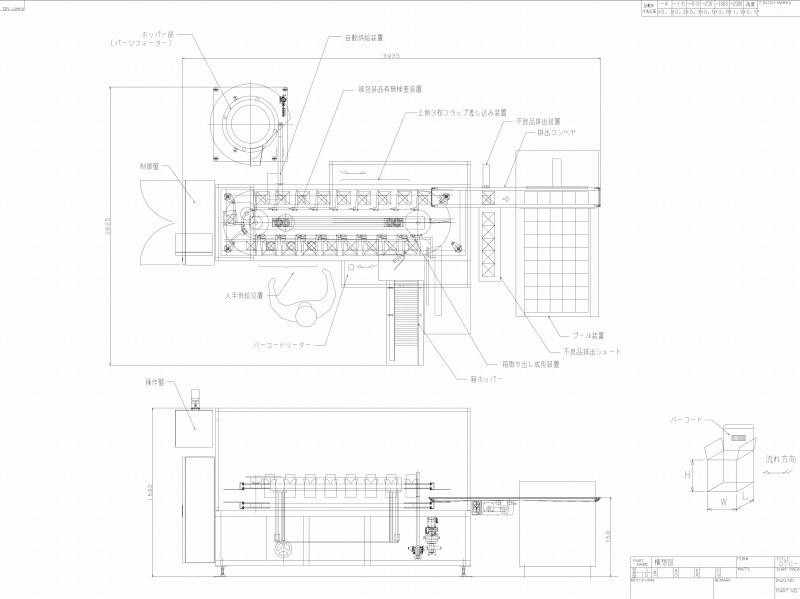
- 箱成形
- ワーク投入、付属品投入
- プラグ投入
- 中身有無検査
- 封函
- ラベル貼り
- 集積
※青枠は当社導入範囲
お客様の課題
フィルター部品を製造されているお客様より、箱詰め・包装工程を自動化したいというご要望を頂戴しました。自動化にあたり、お客様は以下の課題をお持ちでした。
1)投資できる予算が限られているため、予算内に収まる費用で、最大限の省人化を実現できるラインを導入する
2)多品種生産であり、多品種に対応できる自動化ラインを導入する。また、段取り替えの時間を最小限とし、多品種生産による稼働率の低下を回避する
3)人手が介入する工程がある場合、ヒューマンエラー発生時の不良品出荷リスクを回避する
小箱包装工程の自動化実績を豊富にもち、また全自動~半自動まで柔軟に提案できる点を評価いただき、当社をご選定いただきました。
提案・導入内容
当小箱包装ラインは、箱成形 → ワーク投入、付属品投入 → プラグ投入 → 中身有無検査→封函→ラベル貼り→集積の構成となっています。
1)の課題について、予算内に収めるためフィルター部品や付属品は手動投入する仕様にて提案しました。一方で、プラグ投入は自動化しています。フィルター部品や付属品は多品種であり、自動化を行う場合に初期コストが増大するため、自動化が可能であり入れ忘れ発生リスクが高いプラグを自動投入としています。
2)の課題では、上記の通り、多品種対応を前提としたライン構成にしています。段取り替えについては、箱抑えユニット、箱グリップの爪調整をインジケータで行う仕様とし、最大限、段取り替え部品を少なくした仕様にて導入しています。また、工具レスでの段取り替えを実現し、段取り替え時の部品脱落回避等、効率を意識して装置開発を行っています。
3)の課題に関して、内容物有無検査の機構を搭載し、ストッカーへの搬送時に不良排出を自動で行うことができる仕様としています。
導入効果
新設ラインの導入案件としてご用命いただきましたが、小箱包装ラインの導入後、作業者を3人から1人に削減でき、省人化を実現しました。また不良品出荷リスクも回避したことで、生産工程を要因とするクレーム発生数も低減することができました。
将来的な全自動化を考慮したライン設計としており、さらなる生産性向上を目指した事例となります。
ケーサー・カートナー 課題解決.comを運営する日本自働精機は、当事例のように、難度の高い製品の箱詰めラインの半自動化・自動化を全体レイアウトの設計から特注設備の設計開発まで一貫して対応しております。多困難な課題をお持ちの皆様、お気軽に当社にご相談ください。
当事例のピックアップ機器