課題解決・導入事例
駆動部品用箱詰め・包装ライン
- 対象ワーク
- 駆動部品
- 対象ワークサイズ
- ー
- 箱サイズ
- W66~185 L66~185 H22~65
- 箱種類
- 天地3枚フラップ差込
- 生産能力
- 常用20カートン/分
- 納入業界
- 工業
全体ライン工程
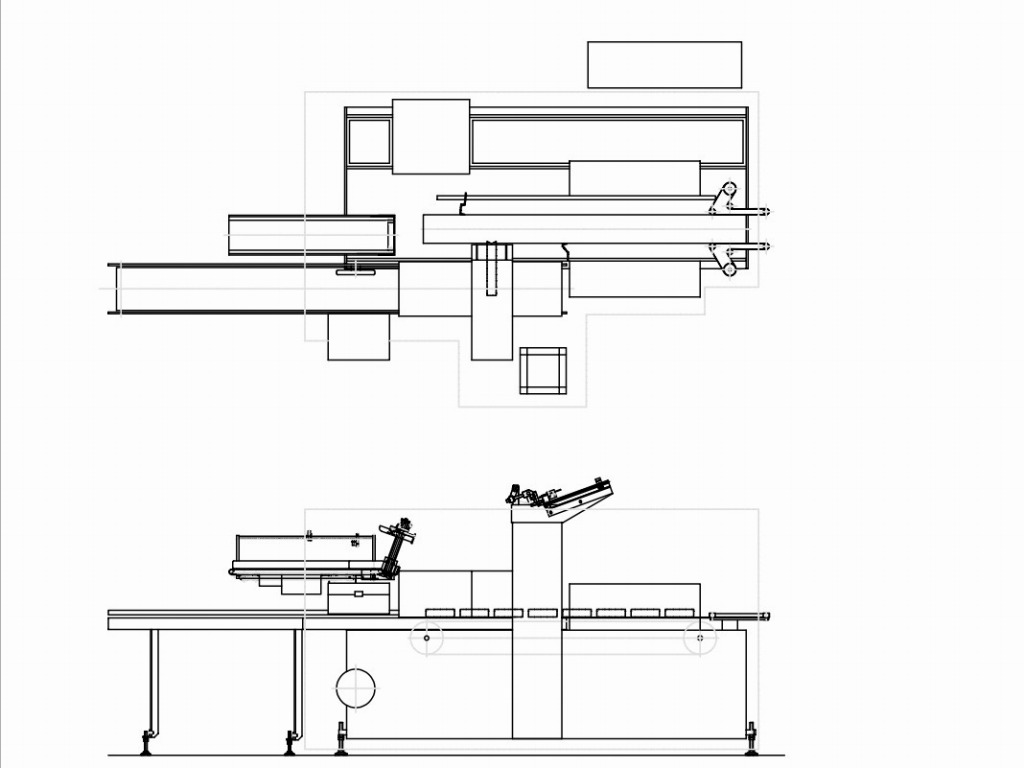
- 搬送
- 箱成型
- 製品投入
- 能書投入
- 封函
- 箱搬送
※青枠は当社導入範囲
お客様の課題
駆動部品を製造しているお客様より、駆動部品の箱詰めライン自動化に関するご相談を頂戴しました。箱詰めラインの導入にあたり、お客様は以下の課題をお持ちでした。
1)本設備で対応する製品サイズの種類が多いが、生産数やスペース等の兼ね合いから複数台の設備での自動化ではなく、1台で多品種の箱詰めが出来る装置を導入し、自動化を実現したい。
2)前述の通り多品種少量生産の為、設備1台で自動化を実現した場合でも、型替えの時間が多く発生してしまう事が予想された。そのため、型替え時間を短縮することで、生産性を向上させる。
3)自動化にあたっての予算が限られており、最大限初期コストを低減し自動化を実現する。
箱詰めする製品はMAXφ180・重量3kgとサイズ・重量共に対応できる標準機がありませんでした。そのため、複数のメーカー様にご相談をされておりましたが、箱詰め自動化ラインの導入実績を多く持ち、お客様の設備仕様・納期の条件を満たした提案を行った当社をご選定いただきました。
提案・導入内容
当箱詰めラインは
①搬送→②箱成型→③製品投入→④能書投入→⑤封緘→⑥箱搬送
の構成となっています。
1)の課題についてですが、W66~185 、L66~185、 H22~65と製品サイズに幅がありましたが、箱の供給ガイドを可変式にし、供給時の箱ズレを防止するなどの対策を行うことで、1台のカートナーでの自動化を実現しました。
2)の課題についてですが、型替え時間を短縮するために、オールサーボでの型替えマシンを提案・納入しました。オールサーボにする事で、段取り時間含めて型替えの時間を最小限とし、トータルの方替え時間を3分でできる仕様を実現しました。
3)の課題についてですが、機器内部の設計も見直し、部品点数を少なくしてシンプルな構造にしました。また、コストダウンのため各構成部品を見直し、予算内での自動化を実現しました。
導入効果
当時例はサイズの異なるワークに対応できる兼用箱詰め装置であり、お客様のご要望にお応えしたことで大変満足頂いた事例となります。
ケーサー・カートナー 課題解決.comを運営する日本自働精機は、当事例のように、特殊な箱詰めの自動化事例を数多く持ちます。特注自動機や特注カートナーの設計開発に強みをもち、お客様の各製品にあった特注自動機の提案をさせて頂きます。困難な課題をお持ちの皆様、お気軽に当社にご相談ください。
当事例のピックアップ機器